Mastering the Craft: Expert Tips for Flawless Light Weight Aluminum Spreading Results
In the world of light weight aluminum know-how, accuracy and casting are vital to attain remarkable outcomes. Grasping the craft calls for a thorough understanding of the devices and tools at one's disposal, a keen eye for preparing the aluminum alloy to specific specs, and an ingenious hand in utilizing optimal spreading methods.
Important Devices and Tools
Aluminum spreading requires certain tools and devices to make sure accuracy and effectiveness in the process. The crucible, typically made of graphite or ceramic materials, stands up to high temperatures needed to thaw light weight aluminum. The mold and mildew, usually made of steel or sand, shapes the liquified light weight aluminum right into the wanted kind.
Additionally, tools like aprons, tongs, and gloves are required to make sure the safety of operators dealing with molten light weight aluminum. Tongs supply a safe and secure grasp when managing warm crucibles and mold and mildews, while heat-resistant handwear covers and aprons safeguard versus accidental burns. Appropriate air flow systems are additionally vital to eliminate fumes and make certain a secure workplace. Buying top notch devices and tools not only improves the precision of aluminum spreading but additionally adds to an extra reliable and risk-free production process.
Preparing the Light Weight Aluminum Alloy
To make certain the success of the aluminum spreading procedure, thorough prep work of the alloy is paramount. The initial step in preparing the aluminum alloy is to carefully select the ideal kind of light weight aluminum based on the characteristics required for the final product.
After cleansing, the next crucial action is to warm the light weight aluminum to the proper temperature level for casting. Generally, thorough prep work of the aluminum alloy sets the foundation for a successful casting procedure and high-quality end outcomes.
Optimal Casting Strategies
Implementing exact casting strategies is crucial for accomplishing top notch outcomes in aluminum casting procedures. The aluminum must be heated up to the optimum temperature level to lower problems like shrinking and porosity in the last actors.
Furthermore, keeping constant putting rate and stress is key to attaining harmony in the cast item. Steady and sluggish pouring helps stop disturbance and air entrapment, which can bring about flaws. An additional essential facet is using degassing representatives to get rid of contaminations and gases from the liquified aluminum, leading to a cleaner end product.
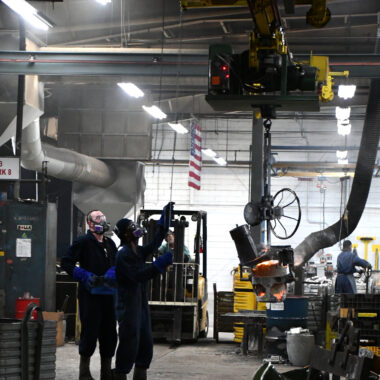
Achieving Smooth Surface Area Finishes
For producers seeking to boost the visual charm and high quality of their aluminum spreadings, attaining smooth surface coatings is an important element following exact casting strategies and proper air conditioning procedures. One key approach to attain smooth surface area finishes is by utilizing high-grade molds that are appropriately prepared and kept. The mold surface area should be diligently cleaned and covered with launch agents to avoid imperfections transferring onto the actors aluminum during the cooling process.
Moreover, regulating the air conditioning rate of the aluminum casting is vital for achieving a smooth surface coating. Fast air conditioning can lead to thermal slopes that cause surface defects, while check out here slow-moving cooling might trigger microstructural company website issues - aluminum casting illinois. By applying regulated air conditioning processes, such as making use of air or water quenching techniques, producers can guarantee that the aluminum strengthens uniformly, minimizing the probability of surface area blemishes
In addition to mold top quality and cooling treatments, post-casting therapies like shot blasting or chemical etching can better refine the surface coating of aluminum spreadings. These strategies aid smooth out any type of remaining roughness or impurities, causing a remarkable appearance that satisfies the finest standards.
Quality Assurance and Troubleshooting
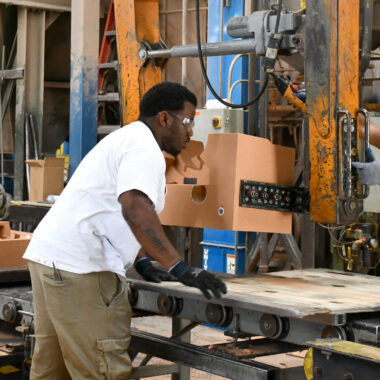
In the world of troubleshooting, it is important to have a comprehensive understanding of typical defects that can occur during light weight aluminum spreading, such as porosity, shrinking, or surface area abnormalities. By performing origin reason evaluation and implementing restorative measures, makers can avoid these defects from reoccuring in future spreading runs. Reliable troubleshooting not just boosts the general high quality of actors aluminum products however also boosts procedure effectiveness and decreases manufacturing expenses. Continuous renovation via quality assurance and repairing techniques is essential to achieving flawless outcomes in light weight aluminum spreading.
Final Thought
Finally, understanding the craft of aluminum casting needs essential devices and equipment, correct preparation of the aluminum alloy, optimal spreading strategies, accomplishing smooth surface area coatings, and carrying out high quality control steps. By complying with these professional ideas, perfect outcomes can be accomplished in aluminum click here now casting procedures. Quality control and troubleshooting are vital facets to think about to ensure constant and top notch cause aluminum spreading tasks.
The initial action in preparing the light weight aluminum alloy is to very carefully pick the appropriate kind of light weight aluminum based on the features required for the last item.Implementing precise casting techniques is necessary for attaining premium results in aluminum casting processes. By grasping these optimal spreading methods, makers can constantly produce perfect light weight aluminum spreadings.
For manufacturers looking for to boost the aesthetic charm and quality of their light weight aluminum castings, accomplishing smooth surface area coatings is a vital aspect complying with specific casting strategies and proper cooling procedures.In final thought, grasping the craft of aluminum casting needs crucial tools and devices, correct prep work of the aluminum alloy, optimum casting strategies, achieving smooth surface coatings, and implementing top quality control measures.